What is Metal Fabrication and How Has It Evolved?
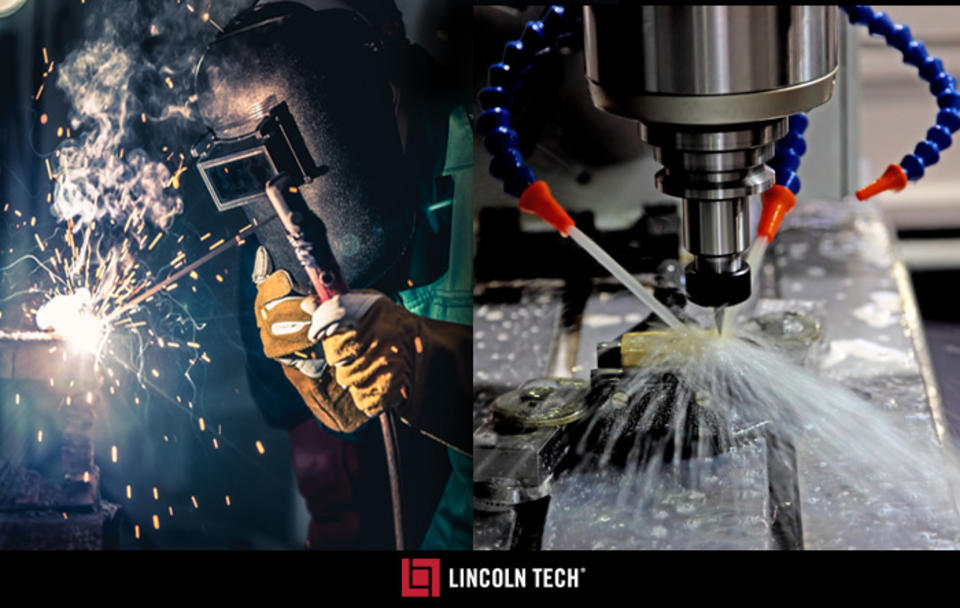
The global metals industry supplies both raw material and metal stock in various compositions, shapes, grades and quantities to manufacturers and consumers around the world. As of 2023, this industry is valued at over $8 trillion dollars, and is growing at an annual rate of 7.8% 1. This raw metal stock is used by experts called metal fabricators to create an endless list of useful products for society.
The art and science of metal fabrication is vital for society. Simply put, someone needs to turn that bare metal into a useful and reliable product to fit consumer demand. And that takes specific skills to achieve. This is where the metal fabricator comes in.
What is Metal Fabrication?
Old-World Metal Fabrication
The definition of metal fabrication can be very broad because it can represent almost any method of crafting with metal. We can start with the Bronze Age, where people began melting tin and copper and mixing them together to gain the useful traits of the resulting metal alloy. This age represents mankind’s earliest use of fire to convert two metal ores into their molten states and then mix them together to create a new material. The Iron Age followed the Bronze Age, which ushered in the creation of new tools and weaponry. Blacksmiths forged iron shafts into swords using high heat and hammers, thus creating the process of forging metal into useful shapes.
Metal Fabrication in the Industrial Age
Jump forward to the 19th and 20th centuries, and the production of high quality steel and alloyed steels became a massive industry in its own right. The output from steel companies were then used by designers and skilled craftsmen to build ships, locomotives, boilers, skyscrapers, bridges and countless other items. As the quality and different compositions of metal grew, so did the processes used to fabricate new and useful items. This gave us the Industrial Age, and the flow of new & cutting-edge metal products became the norm.
The Industrial Age is Still Here & it Has Improved Immensely
The Industrial Age did not actually end when the Information Age appeared. Instead, it morphed into a globe-spanning array of related industries, where cleaner, safer and more efficient work environments are the norm. The dusty machine shops of yesteryear have been largely replaced by clean factory floors, and high-precision machinery with sealed work areas and redundant safety devices. Industry in the 21st century is making more advanced products in a safer and more environmentally-friendly way.
Safety & Efficiency in Metal Fabrication Environments
A big factor in today’s heavy industry versus the previous centuries is that the principles of worker safety and environmental stewardship have been added. Results include recycling and reclamation of old metals, sophisticated and capable HVAC and air filtration systems in factories, and more efficient and safer machinery run by companies whose environments are overseen by OSHA, the Occupational Safety and Health Administration2. In turn, these cleaner, safer and more efficient environments give the skilled metal fabricator the best environment to produce the more advanced products.
Interestingly, many of the skilled jobs from the 19th and 20th centuries are still with us. We still use riveters and welders in heavy construction – there is not a bridge made or rebuilt today that doesn’t use these skills. The same skills are needed to build and maintain ships and aircraft.
Machinists have mostly moved on to CNC programming and manufacturing, proving that these skills are as needed now as they were when they first appeared. The difference is that they are now done with more advanced equipment that yield more accurate results, and do so under the safest possible conditions by technicians who have developed their skills under rigorous training conditions and standards.
Metal Fabrication Can Include Multiple Disciplines
In the U.S. heavy industries and consumer product divisions, metal fabrication often combines multiple disciplines. Sometimes a product starts as a metal forging, and is then passed to a machine shop for close-tolerance machining. The output might then be welded or riveted to other items to create a complex structure as the finished product.
The finished product depends on the end-use by the consumer. Regardless of use, the technology and skill of the person crafting the metal dictates the quality of the goods. The range of products is practically limitless, and can be as complex as an airliner or as simple as a teaspoon. The processes used to create these two disparate products are as different as the products themselves.
An airliner will require welding of ferrous and non-ferrous metals, as well as extremely high-precision machining and/or specialized forging of complex components. A teaspoon might just require being cast, stamped or forged from a single piece of metal, and the complexity simply dependent on the production skills and equipment used by the flatware maker. While they both might share the basic forging process, these two products couldn’t be more different in their metal fabrication process or their use by the consumer.
Welding and machining do not include the forging process as a step, however, as forged products sometimes require welding or machining to prepare as a finishing step in the assembly of a finished product.
Today, the metals most used in industry include aluminum, brass, copper, gold, iron, nickel, silver, magnesium, tin, titanium and various compositions and grades of steel.
Metal Fabrication is a Skill in High Demand
With the manual processes of the past being largely replaced through the programming of high precision designs into a specialized computer, and directing a digitally-controlled machine to manufacture the part, metal products can be created by a CNC Programmer/Operator.
This mode of manufacturing is called computerized numerical control, or CNC, and uses the G-Code language and syntax to apply a sequence of commands that control the movement, speed and pressures assigned to a cutting tool. This is always done in accordance with a detailed blueprint that has been translated by the CNC technician into G-Code. The machine processes the g-code and in turn mills a finished product from a metal block, rod, plate or casting. Done correctly, the finished piece should match the blueprint within a very close and specific tolerance.
The process just described had long been one of the most difficult functions to automate. Now that computerized machine control has been developed, the field has been growing steadily. The demand for skilled CNC programmers & CNC tool operators exceeds 200,000 jobs nationwide, with 143,000 job openings for CNC operators projected out to 2032, and 32,000 job openings for CNC programmers in the same time period3,4. CNC Programmers are considered to have a bright outlook by the Bureau of Labor Statistics4. These jobs are a crucial component of the manufacturing vertical of the United States which employs over 12 million individuals.
Regardless of the use of the end-product, metal fabrication is as relevant to the economy as it was a century ago, and the demand for precision goods will always exist. The big difference is that the technology used and the safety requirements that have been mandated have dramatically improved. This skill trade has been, and will remain, a lucrative and fascinating talent in high demand for the foreseeable future.
1 Metal And Mineral Global Market Report 2023, found at https://finance.yahoo.com/news/metal-mineral-global-market-report-124400977.html, Published by A, Jiangxi Copper Company, Votorantim S.A, JFE Holdings Inc., and LafargeHolcim Ltd.on April 21, 2023 in Yahoo Finance. Retrieved on September 6, 2023.
2 The Occupational Safety and Health Administration is a part of the U.S. Department of Labor, and can be found at https://www.osha.gov/
3 National Center for O*NET Development. National Employment Trends: 51-9161.00 - Computer Numerically Controlled Tool Operators. O*NET OnLine. Retrieved December 5, 2023, from https://www.onetonline.org/link/localtrends/51-9161.00.
4 National Center for O*NET Development. National Employment Trends: 51-9162.00 - Computer Numerically Controlled Tool Programmers. O*NET OnLine. Retrieved December 5, 2023, from https://www.onetonline.org/link/localtrends/51-9162.00.